Für die Verarbeitung von Thermoplasten und Polyurethan in einem Bauteil existieren Sonderverfahren, die als Spritzguss-RIM-Kombinationsverfahren bezeichnet werden können. Dabei wird das Spritzgießverfahren für die Verarbeitung eines thermoplastischen Kunststoffs verwendet. Polyurethan wird hingegen im RIM-Verfahren verarbeitet.
Spritzgießen
Beim Spritzgießen handelt es sich um ein Urformverfahren, bei dem ein thermoplastischer Kunststoff zunächst aufgeschmolzen (plastifiziert) wird und danach in flüssiger Form in ein Werkzeug injiziert wird. In der Kavität kühlt der Thermoplast ab und erstarrt.
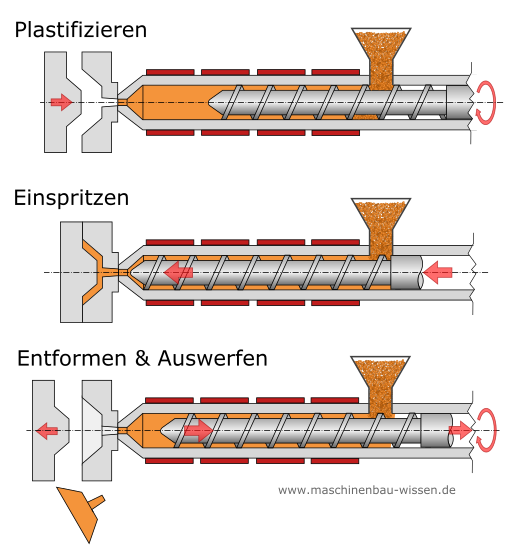
Ablauf des Spirtzgießverfahrens
RIM-Verfahren
Beim RIM-Verfahren (=Reaction Injection Moulding) werden zwei flüssige Komponenten vermischt, welche in Mischung zu einem Polyurethan ausreagieren. Das Vermischen erfolgt in einem speziellen Mischer, der vor der Kavität angeordnet ist. Das Gemisch wird in ein Werkzeug injiziert, in dem die Aushärtung des Materials erfolgt.
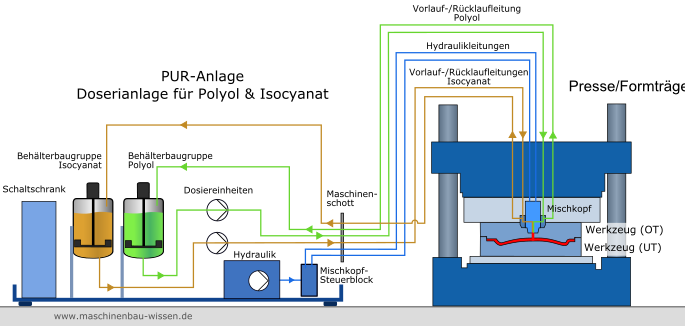
Anlage für das RIM-Verfahren mit Polyurethan
Kombination von Spritzguss- & RIM-Verfahren
In verschiedenen Anwendungen wird das Spritzguss- und RIM-Verfahren miteinander kombiniert. Es wird hierbei zunächst ein Thermoplast-Bauteil per Spritzgießen hergestellt, welches dann zunächst im Werkzeug verbleibt. Das Werkzeug verfügt entweder über einen verfahrbaren Stempel, der die Kavität nach dem Erstarren des Spritzgussteils erweitert oder es handelt sich um ein Wendeplattenwerkzeug, das auf der Gegenseite eine Formhälfte mit erweiterter Kavität besitzt.
In jedem der beiden Fälle ist durch die Erweiterung der Kavität im zweiten Schritt eine Applikation von Polyurethan möglich. Das PU kann dabei über die gesamte Oberfläche des Werkstücks gegossen werden, oder auch nur über einen Teilbereich. Auch die Funktion der PU-Schicht kann unterschiedlichen Zwecken dienen.
Anwendung von Spritzguss-RIM-Kombinationsverfahren
Mit der Kombination aus Spritzguss- und RIM-Verfahren können Bauteile hergestellt werden, die einen solide Grundstruktur aus Thermoplast aufweisen und eine weich geschäumte Oberfläche aus Polyurethan. Man spricht hier auch von Soft-Touch-Oberflächen, die oft im Automobil-Innenraum eingesetzt werden, z.B. für Armaturenbretter oder Tür-Verkleidungen.
Es kann hierbei auch eine Dekorfolie eingesetzt werden, die über der Polyurethanschicht angebracht ist und Optik und Haptik verbessert. Es entstehen auf diese Weise besonders hochwertige Interieur-Oberflächen.
Schema einer Gesamtanlage für Spritzguss-RIM-Kombiverfahren
Eine andere Anwendung der Kombinationsverfahren von Spritzguss und Polyurethan ist die Aufbringung von weicheren, rutschfesten Flächen, die als Grifffläche dienen. Beispielsweise kann der Griff einer Bohrmaschine durch das etwas weichere Polyurethan grifffest gestaltet werden, während der Grundkörper aus stabilerem thermoplastischen Kunststoff besteht.
Auch das Beschichten mit Farbe bzw. Lack auf PU-Basis ist eine Anwendungsvariante der Kombi-Verfahren. Bauteile, die auf diese Weise gefertigt werden, können zum Beispiel als Fahrzeug-Außenteile (Verkleidungsteile) eingesetzt werden.
Anlagentechnik der Spritzguss- & RIM-Kombiverfahren
Um ein Spritzguss-RIM-Kombiverfahren anwenden zu können benötigt man eine aufwendigere Anlagentechnik, als dies beim einfachen Spritzgießen der Fall wäre. Zur standardmäßigen Spritzgießmaschine wird zusätzlich eine Dosiermaschine für Polyurethan mit entsprechendem Mischaggregat benötigt.
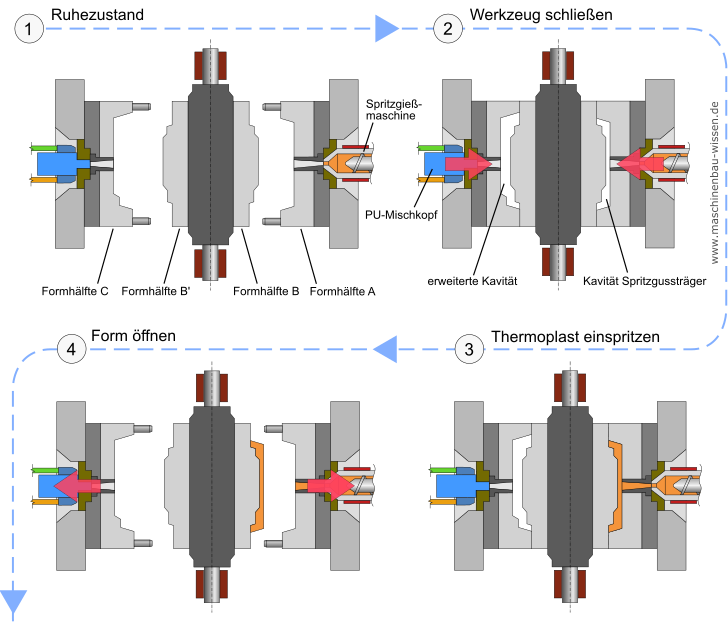
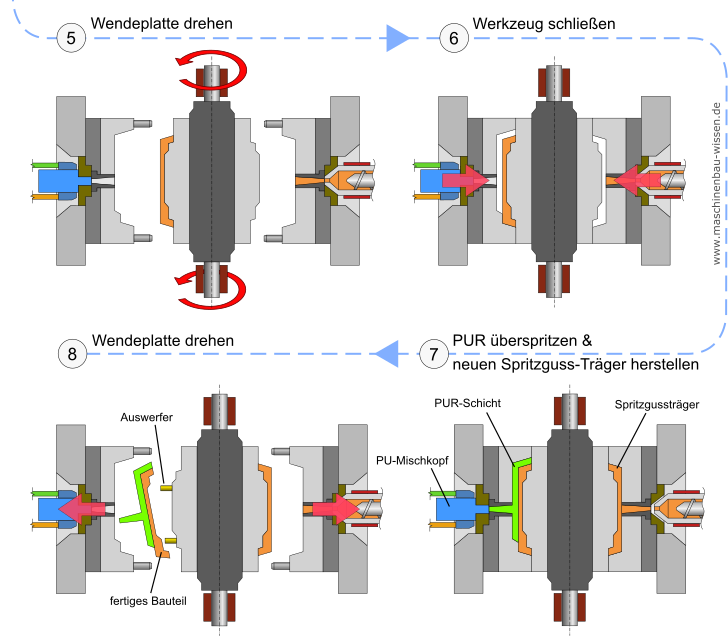
Spritzguss-RIM-Kombi-Prozess in 8 Schritten
Auch die Werkzeugtechnik ist komplexer, da man für die Beschichtung mit Polyurethan die Kavität nach dem Spritzgießprozess erweitern muss. Wie bereits beschrieben, wird hierfür entweder ein Werkzeug mit Schieber oder ein Wendeplattenwerkzeug benötigt. Bei Werkzeug mit Schieber fährt nach dem Spritzgießprozess ein Stempel im Werkzeug zurück und erweitert dadurch die Kavität. Beim Wendeplattenwerkzeug hat man eine drehbare Aufspannplatte, die eine Werkzeughälfte trägt – gegebenenfalls auch eine auf jeder Seite. In dieser Werkzeughälfte verbleibt das Bauteil nach dem Spritzgießen. Die Aufspannplatte dreht sich dann zusammen mit der Werkzeughälfte um 180° und bildet mit einer zusätzlichen Formhälfte eine neue Kavität, die Raum für die PUR-Schicht bietet. Während dem Überfluten mit PU kann auf der Gegenseite bereits ein neues Spritzguss-Trägerteil gegossen werden (zumindest soweit die drehbare Aufspannplatte auf beiden Seiten mit einer Werkzeughälfte bestückt ist).
Vorteil dieser Anlagentechnik ist, dass man hochwertige Bauteile sehr wirtschaftlich herstellen kann, da beide Prozessschritte (Spritzen und Schäumen) auf einer Anlage stattfinden. Hierdurch wird auch der Platzbedarf klein gehalten.