Das Sprühen von Polyurethan ist eine Methode der Verarbeitung dieses duroplastischen Kunststoffs. Beim Sprühprozess wird der noch flüssige Kunststoff mit Hilfe einer Düse zerstäubt und in ein offenes Werkzeug oder auf ein Halbzeug aufgetragen. Das Polyurethan härtet daraufhin aus und bildet so ein festes Werkstück. Die Möglichkeiten der Anwendung des PUR-Sprüh-Verfahrens sind dabei sehr vielfältig.
Herstellung Polyurethan
Polyurethan wird durch Vermischen eines Polyols und eines Isocyanats hergestellt. Die beiden Komponenten reagieren daraufhin in einer Polyaddition zu einem festen, duroplastischen Kunststoff. Je nach verwendetem PUR-System und Mischungsverhältnis ist es möglich die spezifischen Eigenschaften des Kunststoffs (wie Dichte, Formfestigkeit, Oberflächenstruktur, Brandverhalten, Isolierfähigkeit, etc.) anzupassen.
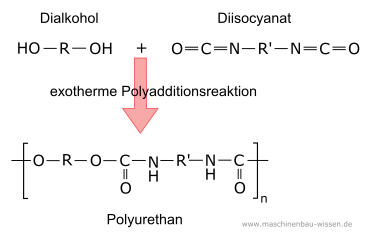
Polyadditionsreaktion zu Polyurethan
PUR-Sprüh-Verfahren
Beim PUR-Sprüh-Verfahren werden zunächst die beiden Reaktionspartner – Polyol und Isocyanat – in einem sogenannten Mischkopf homogen vermischt. Die Vermischung findet unter hohem Druck statt (bis zu 200bar). Das Reaktionsgemisch wird dann unter geringerem Druck (ca. 16 bar) zusammen mit Druckluft durch eine Sprühdüse gedrückt und dadurch zerstäubt. Die verwendeten PU-Systeme können für das Verfahren geschäumt, kompakt, gefüllt oder auch ungefüllt sein.
Hochdruck-Mischköpfe nach dem Stand der Technik kommen ohne Mischelement aus und sind somit sehr leicht zu reinigen, was die Standzeit der Sprühelemente erhöht. Häufig sind die Mischeinheiten auch selbstreinigend. Der Einsatz von High-Speed-PUR-Systemen ist somit kein Problem. Mit Hilfe von speziellen Hartmetall-Mischköpfen ist es zudem möglich abrasive Füllstoffe wie Bariumsulfat oder Kreide zuzumischen. Der Füllstoffgehalt im Bauteil kann dabei bis zu 75 % erreichen.
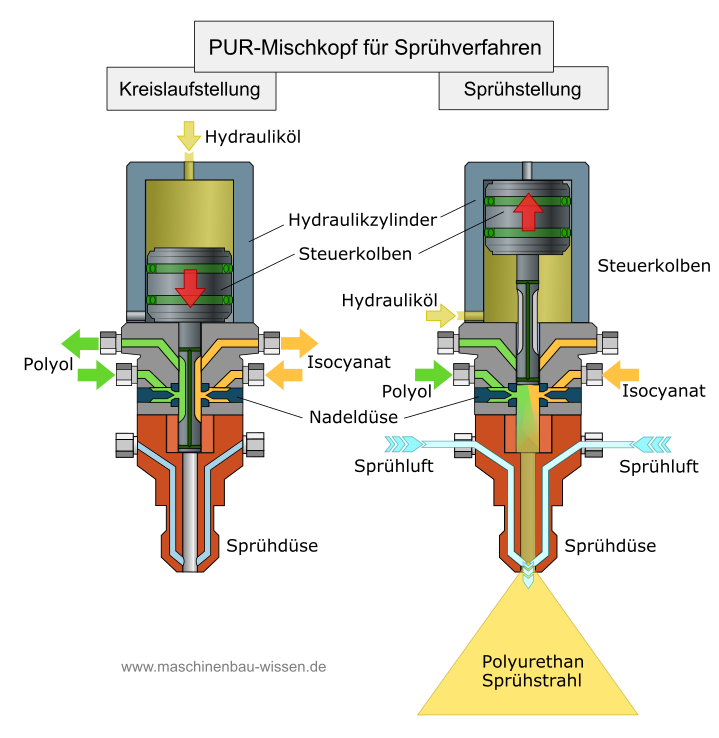
Schnittdarstellung eines PUR-Mischkopfs für das Sprühverfahren
links: Kreislaufstellung für Poly & Iso | rechts: Schusstellung
Je nach Anwendungsfall wird der PUR-Sprühstrahl auf eine Werkzeughälfte oder ein Halbzeug aufgetragen. Der Mischkopf kann hierzu von einem Industrie-Roboter geführt werden, um den Grad der Automation zu erhöhen. Ziel dabei ist ein gleichmäßiger, dünner und zumeist großflächiger Auftrag mit geringem Overspray. Als Overspray wird dabei der dünne Sprühnebel bezeichnet, der sich an den Rändern des Sprühstrahls bildet.
Der Durchmesser des Sprühstrahls wird über den Abstand des Mischkopfs zum Bauteil variiert. Für großflächige Bauteile kann der Abstand auf bis zu 1000mm eingestellt werden, um eine schnelle Formfüllung zu realisieren. Die Austragsleistung kann je nach Produkt zwischen 10 und 200g/s betragen.
Kommen neben dem PUR auch geschnittene Fasern (Naturfasern od. Glasfasern) zum Einsatz, spricht man von sog. Fasersprühen bzw. Faserspritzen. Für diese Anwendungen wird ein Faserschneidwerk in der Nähe des Mischkopfs angebracht, das die Fasern in die gewünschte Länge bringt und in den Sprühstrahl des Mischkopfs fördert.
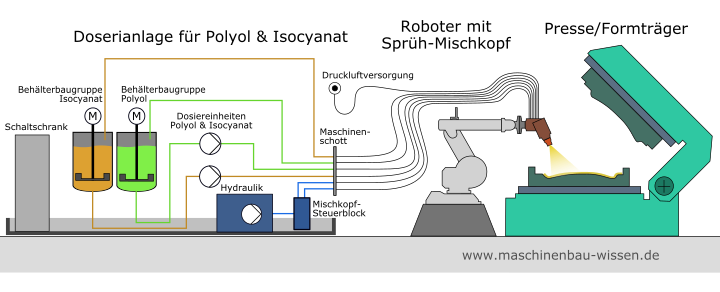
Schematischer Anlagen-Aufbau für den PUR-Sprühprozess
Quellen für diesen Artikel:
- https://www.dbu.de/123artikel29521_2430.html
- https://www.kunststoffe.de/produkte/uebersicht/beitrag/pur-csm-spruehtechnik-vielseitig-spruehen-573332.html
Vorteile beim Sprühen von Polyurethan
Im Vergleich zu anderen PUR-Verfahren (wie zum Beispiel RIM) hat das PUR-Sprühen den Vorteil, dass das Material großflächig und gleichmäßig in ein offenes Werkzeug appliziert werden kann. Dies hat den Vorteil, dass keine großen Drücke entstehen und somit die Kosten für Werkzeug und Presse (bzw. Formenträger) gering bleiben. Auch aufwändiges Entlüften und weitere Nacharbeiten sind nicht mehr nötig.
Da der Einsatz von hochreaktiven PUR-Systemen möglich ist, reduzieren sich zudem die Zykluszeiten. Stand der Technik sind gegenwärtig Aushärtezeiten von drei Minuten, wonach man das Bauteil entformen kann. Die Fertigung kann heute völlig frei von Styrol und Lösemitteln bleiben, womit das PUR-Spritz-Verfahren eine umweltfreundliche Alternative zu glasfaserverstärkten Kunststoffen (GFK) aus styrolhaltigen Polyesterharzen ist. Ein weiterer Vorteil ist, dass man sehr dünne Schichten erzeugen kann und auch die Darstellung von komplexen Geometrien möglich ist. Die Schichtdicken sind konstant und die hergestellten Oberflächen hochwertig.
Zusammenfassung der Vorteile
- Sprühen von PUR großflächig und gleichmäßig
- Eintrag ins offene Werkzeug, dadurch geringere Kosten für Werkzeug und Presse
- Abbildung von komplexen Geometrien
- Herstellung von hochwertigen Oberflächen
- Besprühen von Halbzeugen möglich
- Einsatz von High-Speed-PUR-Systemen, dadurch reduzierte Zykluszeiten
- Einsatz von Verstärkungsfasern möglich
- PUR-Sprüh-Verfahren ist sehr vielseitig einsetzbar
- Lösemittel- und styrolfreie Fertigung möglich
Anwendung des PUR-Sprüh-Verfahrens
Für das PUR-Sprüh-Verfahren existiert eine Vielzahl von Anwendungsmöglichkeiten. Typisch ist zum Beispiel das Sprühen von Häuten (sog. PU-Sprühhäute), wobei auch sogenannte PUR-Soft-Touch-Oberflächen hergestellt werden können. Gesprühte Polyurethan-Häute können auch so gestaltet werden, dass diese kaum noch von echtem Leder zu unterscheiden sind.
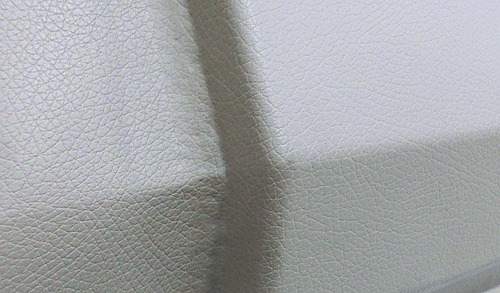
Kunstleder hergestellt mit PUR-Sprühverfahren
Daneben werden ebenso schalldämmende Bauteile und Coatings mit der Sprühtechnik hergestellt oder das Verfahren für das Auftragen von PUR als Klebesystem eingesetzt - z.B. beim Laminieren von Platten für die Möbelindustrie.
Ein weiteres Anwendungsfeld für das Verfahren sind Sandwichelemente mit einem Wabenkern und faserverstärkten Außenschichten, die im Sprühprozess mit PU getränkt werden. Auch Strukturelemente können durch den Einsatz von Verstärkungsfasern hergestellt werden. Verwendet werden hierfür Glas- oder Naturfasern. Bei den Anwendungen mit geschnittenen Fasern ist auch vom Fasersprühen bzw. Faserspritzen die Rede. Es kommen dabei spezielle Faserschneidwerke zum Einsatz, welche die Fasern in gewünschter Länge schneiden und diese in den Sprühstrahl des Mischkopfs fördern.