Grundsätzlich werden Kunststoffe (auch Plaste) hergestellt, indem man Monomere schrittweise zu längeren Ketten, den so genannten Polymeren, aneinander fügt. Dabei unterscheidet man zwei Arten der Polymerisation: die Kettenpolymerisation und die Stufenpolymerisation.
Während der Kettenpolymerisationen wachsen die Molekülketten durch das sukzessive Hinzufügen weiterer Monomere. Dabei wird das Molekül, welches die Polymerisation startet, als Initiator bezeichnet, während ein auf dem Initiator aufwachsendes Molekül als Monomer bezeichnet wird. Aus wie vielen Monomeren das fertige Polymer besteht, hängt von dem Polymerisationsgrad ab. Mathematisch wird der Polymerisationsgrad durch die Mayo-Gleichung abgeschätzt. Außerdem ist der Polymerisationsgrad durch das Verhältnis von Monomer zu Initiator einstellbar.
Zu den Plasten, die durch Kettenpolymerisation entstehen, zählen zum Beispiel:
- Polyethylen (PE)
- Polypropylen (PP)
- Polyvinylchlorid (PVC)
- Polystyrol (PS)
- Polyacrylnitril (PAN)
- Polytetrafluorethylen (PTFE)
- Polymethylmethacrylat (PMMA)
Aus Monomeren entstehen Polymere
Die radikalische Polymerisation
Werden die Wachstumsreaktion zur Herstellung von Kunststoff durch Radikale initiiert und fortgesetzt, spricht man von einer radikalischen Polymerisation. Diese Art der Polymerisation verhält sich im Vergleich mit anderen Kettenreaktionen relativ unempfindlich. Sie ist einfach zu kontrollieren und führt schon bei relativ kleinen Umsätzen zu hohen Polymerisationsgraden. Deshalb wird die radikalische Polymerisation gerne bei der Herstellung preiswerter Kunststoffe, wie PVC, PS oder LD-PE angewandt.
Da die radikalische Polymerisation exotherm ist, kann bei diesem Herstellungsverfahren die durch Polymerisation frei werdende Wärme eine Gefahr darstellen. Wird die so entstehende Wärme nämlich nicht in ausreichendem Umfang abgeführt, werden weitere Radikale erzeugt, welche zu sich selbst beschleunigenden Reaktionen führen kann. Dies kann das Reaktormaterial überlasten und zu thermischen Explosionen führen.
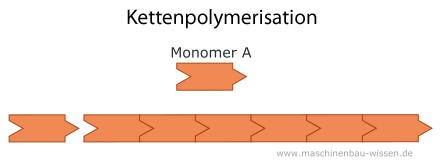
Schematische Darstellung einer Kettenpolymerisation
Die ionische Polymerisation
Initiieren ionische Spezies die Polymerisationen und sorgen für fortgesetzte Wachstumsreaktionen, spricht man von einer ionischen Polymerisation. Dabei sind die wachsenden Ketten mit einer Lebensdauer von mehreren Stunden bis Tagen langlebiger, als durch radikalische Polymerisation entstandenen Molekülketten. Letztere weisen diese auch als lebende Polymere bezeichneten Ketten eine Lebensdauer von 10−3s auf. Mit der Bezeichnung lebend ist vor allem gemeint, dass man den Ketten auch nach Abschluss einer Polymerisation ein weiteres Monomer aufgeben kann, um das Wachstum der Polymere fortzuführen.
Bestehen die Ketten von Polymeren aus zwei oder mehr unterschiedlichen Typen von Monomeren, handelt es sich um so genannten Copolymere. Befinden sich in einem Copolymer lange Blöcke des einen Monomers, denen Blöcke anderer Monomere folgen, spricht man von Blockcopolymeren.
Einen wesentlichen Nachteil bei der Anwendung der ionischen Polymerisation zur Herstellung von Kunststoff stellt der auf Verunreinigungen, Sauerstoff und Wasser empfindlich reagierende Herstellungsprozess dar. Dieser gestaltet sich im Vergleich zu Kettenpolymerisationen mit der radikalischen Polymerisation aufwändiger und kostenintensiver.
Die ionische Polymerisation wird zur Herstellung spezieller Produkte wie beispielsweise Acrylnitril-Butadien-Kautschuk (NBR) oder Styrol-Butadien-Kautschuk (SBR) eingesetzt. Diese synthetischen Gummis werden zum Beispiel zur Produktion von Autoreifen verwendet.
Kettenpolymerisationen mit metallorganischen Katalysatoren
Die beschriebenen Polymerisationen bzw. Kettenpolymerisationen vollziehen sich in Gegenwart von Katalysatoren. Als Katalysatoren setzt man dabei von weiteren Spezies umgebene Verbindungen von Metallatomen ein. Dieser so genannte Metallkomplex bindet die wachsende Kette.
Weitere Monomere kann man durch Insertion des Monomers zwischen die wachsende Kette und die Katalysatorspezies addieren. Die aus diesem Prozess entstehenden Polymere sind einem höheren Ordnungsgrad sowie einem geringeren Verzweigungsgrad zuzuordnen. Diese reguläre Struktur hat eine effizientere Packung der einzelnen Ketten im Festkörper zur Folge, was zu einem dichteren Kunststoff führt. Ziegler-Natta-Katalysatoren stellen aktuell die wichtigste industriell eingesetzte Katalysatorklasse dar. Eingesetzt werden sie beispielsweise bei der Produktion von Polyethylen.
Das so genannte High-Density-Polyethylen wird im Ziegler-Natta-Verfahren unter Verwendung eines metallorganischen Katalysators hergestellt. Aus dem Verfahren gewinnt man ein Polymer mit hohem Ordnungsgrad und wenigen Verzweigungen bei gleichzeitig hoher Dichte. Unter anderem wegen seiner höheren mechanischen Stabilität wird dieser Kunststoff als Werkstoff zum Beispiel zur Herstellung von Benzinkanistern, Autotanks und anderen Behältern genutzt.
Dem gegenüber handelt es sich bei Low-Density-Polyethylen - LD-PE in der Gasphase um polymerisiertes Ethen, das sich durch einen geringen Ordnungsgrad, viele Seitenverzweigungen und geringe Dichte auszeichnet. LD-PE ist deshalb ein Kunststoff, der vor allem zur Herstellung von mechanisch weniger stabilen, transparenten oder gefärbten Verpackungsmaterialien wie Folien und Verpackungen wie Getränkeflaschen verwendet wird.