Chemische und physikalische Prozesse bilden die Grundlage der Herstellung von Polyurethanschaumstoffen (PUR-Schäume). Indem beide Prozesse kombiniert werden, lässt sich ein Schaum produzieren, der den jeweiligen Anforderungen entspricht. Hierfür ist PUR-Chemie ein wichtiger Bestandteil. Sie ermöglicht es durch die geeignete Auswahl und Rezeptur der miteinander reaktionsfähigen Grundkomponenten, bereits im Voraus die molekulare Struktur für das gewünschte Schaumsystem exakt festzulegen.
Herstellung von Polyurethan-Schaumstoff
Man stellt Polyurethan-Schaumstoffe in der Regel durch Vermischen von flüssigen Di- oder Polyisocyanaten mit Polyether- oder Polyesterpolyolen sowie diverser Zusatzstoffe her. Werden zwei flüssige reaktionsfähige Komponenten eingesetzt, spricht man daher vom Reaktionsschaumgießen (sog. RSG-Verfahren). Die Art und die Funktionalität des Polyols sowie das Mischungsverhältnis der Komponenten die Auswahl des Schäumungsverfahrens sowie die gewählten Zusatzstoffe bestimmen die späteren Eigenschaften des PUR-Schaumstoffs.
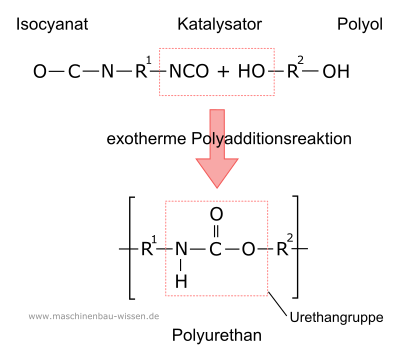
Herstellung von PU (ohne Schäumen durch Treibmittel)
In der Polyurethanchemie werden zahlreiche Zusatzstoffe eingesetzt. Hierbei handelt es sich unter anderem um Katalysatoren, Vernetzer und Farbmittel sowie Treibmittel-Kombinationen, Schaumstabilisatoren, Flammschutzmittel und nicht zuletzt Keimbildner. Hieraus folgt, dass auf diese Art und Weise eine weitgehende Anpassung der Schaum-Eigenschaften an den beabsichtigten Verwendungszweck erfolgen kann.
Der Verfahrensablauf beim Polyurethan-Schäumen
Bei nahezu allen eingesetzten Verfahren zum Polyurethan-Schäumen sind die folgenden Verfahrensschritte notwendig:
- Dosieren
- Förderung und Vermischung der einzelnen Reaktionskomponenten
- Gießen, Sprühen oder Spritzen der fertigen Mischung
- Schäumen (unter Vernetzung: Gelieren) sowie
- Entformung des Schaumsystems
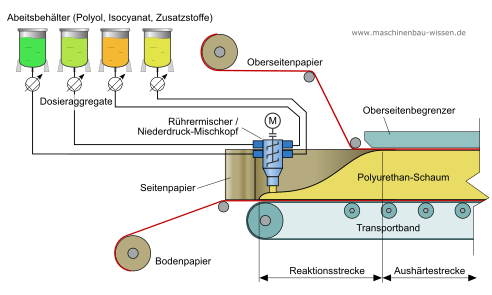
Anlage für das Schäumen von PU
Muster und Kleinserien lassen sich unter Umständen in Handarbeit anfertigen. Hierfür benötigt man Mischgefäße, eine genaue Waage und ein Rührwerk mit hoher Drehzahl. Anschließend gießt man die Mischung in die auszuschäumdenden Hohlräume oder Werkzeuge. Dort erfolgt das Schäumen. Maschinelles Verarbeiten erfolgt entsprechend mit Gießmaschinen. Diese sind mitunter transportabel.
Die Wahl des Dosier- und Mischverfahrens hat großen Einfluss auf das Schaumsystem. Hierbei können Hoch- bzw. Niederdruckanlagen eingesetzt werden, bei denen sich vornehmlich die Mischköpfe unterscheiden. In diesen erfolgt innerhalb kürzester Zeit die Vermischung der Reaktionskomponenten ehe diese in die Formen eingefüllt werden, wo die Masse aufschäumt.
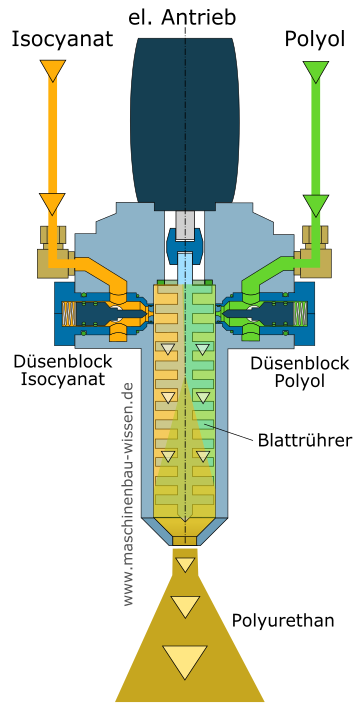
Niederdruck-Mischkopf für das Schäumen von PUR
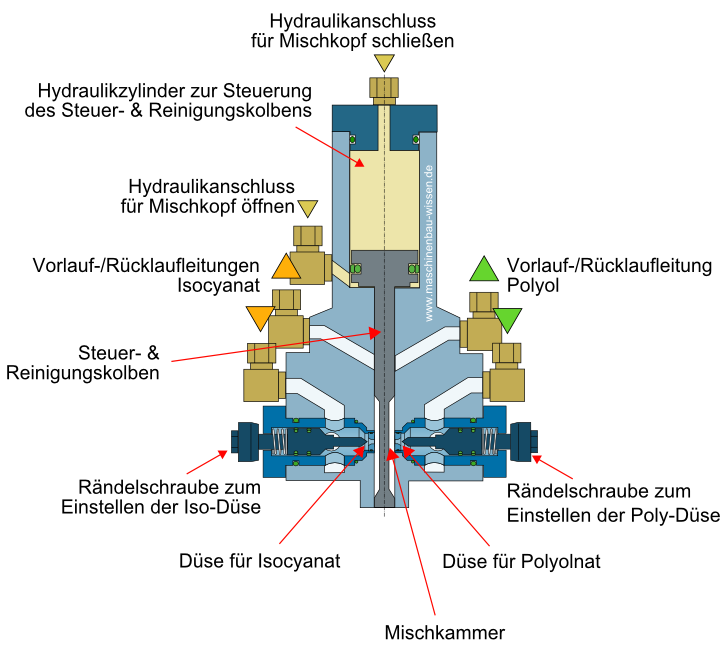
Hochdruck-Mischkopf für das Schäumen von PUR
Die Schaumbildung
Fügt man der Reaktionsmischung eine kleinere Menge Wasser zu, dann reagiert diese mit einem Teil der Isocyanatgruppen. Dabei wird Kohlenstoffdioxid frei. Dieses schäumt die bisher noch weiche Reaktionsmasse auf, wodurch sich der PUR-Schaum bildet. Hierbei reagiert entweder die zuvor entstandene, instabile Carbamidsäure direkt mit einem weiteren Isocyanat direkt zu einem Polyharnstoff. Oder es entsteht zunächst eine primäre Aminogruppe. In einem zweiten Reaktionsschritt reagiert diese zu dem substituierten Harnstoff. Daher führt das freigesetzte Kohlenstoffdioxid nicht zu einem Abbruch der Polymerisation.
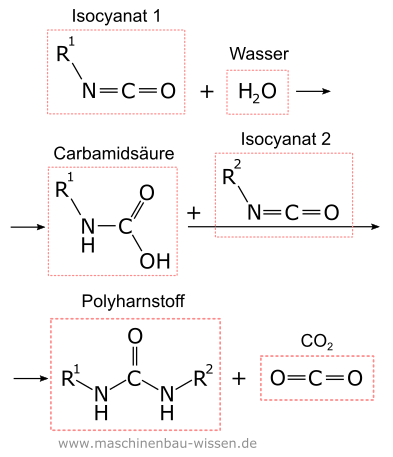
Reaktion von Isocyanat mit Wasser zu einer Polyharnstoff-Gruppe unter Entstehung von CO2
Durch die Menge des dem Reaktion zugegebenen Wassers lässt sich das Raumgewicht beim entstehenden Schaumsystem nahezu beliebig variieren. Durch die Zusetzung von Treibmitteln wird die Herstellung von Polyurethan-Schäumen erst ermöglicht. Durch das Verbot von FCKW-haltigen Treibmitteln erfolgte eine Umstellung der Treibmittel für PUR-Schaum. Es werden stattdessen nun verstärkt Pentane, Methylenchlorid oder auch reines Kohlendioxid als Treibmittel für PUR-Schaum eingesetzt.
Einfluss der Mischköpfe beim Polyurethan Schäumen
Mischköpfe, wie sie in Niederdruckmaschinen eingesetzt werden, eignen sich insbesondere für die kontinuierliche Fertigung von Halbzeugen. Hierzu zählen etwa Blöcke und Platten. Der Mischkopf ist daher in Form einer mechanischen Rührwerksmischkammer ausgeführt. Diese muss, sobald der Schaumvorgang abgeschlossen ist, gereinigt oder gespült werden.
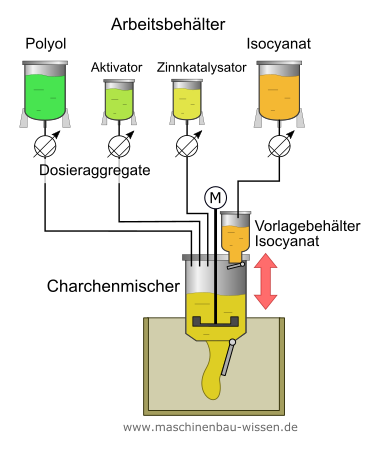
Beispiel für eine Niederdruck-Schäum-Anlage für PU-Blockschaum
Anders ist der Mischkopf in einer Hochdruckanlage konzipiert. Indem man ein Prall- oder Gegenstrom-Mischerprinzip einsetzt, kommt es hier unter Druck zu Injektions- bzw. Strömungsvermischung.
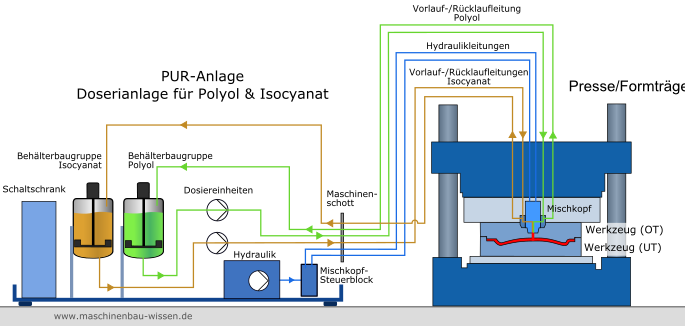
Schematischer Aufbau einer PU-Hochdruck-Schäumanlage mit Presse und Werkzeug
Am Ende des Taktes, dem sogenannten Schussende, wird der Mischkopf mechanisch durch einen Kolben oder Stößel bzw. pneumatisch gereinigt. Hierbei entsteht eine Prozessführung, die starke Parallelen zum Spritzgießen zeigt. Dies gilt vor allem im Hinblick auf den Verbund aus Mischkopf und Werkzeug. Aus diesem Grund wird die diskontinuierliche Fertigung von Formteilen nahezu ausschließlich auf Hochdruckanlagen statt.