Fluidtechnik - Skript
In diesem Online-Skript lernen Sie die Gurndlagen der Pneumatik kennen.
Unter dem Begriff Pneumatik versteht man die Lehre von den Bewegungen und Gleichgewichtszuständen der Luft. Im Bereich der Pneumatik werden Signale, Kräfte und Energie mit Hilfe von Druckluft übertragen, im Gegensatz zur Hydraulik, bei der Füssigkeiten als Medium verwendet werden. Die Pneumatik ist ein Teilgebiet der Fluidtechnik.
In diesem Online-Skript geht es um die Grundlagen der Pneumatik. Der Begriff der Pneumatik hat seine Wurzeln im Griechischen. Pneuma bedeutet zunächst "Wind" oder "Atem", aber auch "Geist". In Wissenschaft und Technik bezeichnen wir die Anwendung und den Einsatz von komprimierter Luft als Pneumatik. In der Pneumatik wird mithilfe von Druckluft mechanische Arbeit verrichtet, Komponenten gesteuert oder es werden Signale übertragen.
Druckluft als Arbeitsmedium
Pneumatik beinhaltet alle technischen Anwendungen, in denen Druckluft als Arbeitsmedium verwendet wird. Im Bereich der Hydraulik dagegen ist das Arbeitsmedium eine Flüssigkeit. Druckluft wurde früher als Pressluft bezeichnet. Sie ist Umgebungsluft, die zunächst angesaugt, dann mittels eines Kompressors komprimiert, anschließend zur Reinigung aufbereitet und dann für verschiedene Zwecke genutzt wird.
Ihren Einsatz erhält sie, neben den typischen Pneumatik-Anwendungen im Anlagenbau, als Aktivluft, um Stoffe zu transportieren wie beispielsweise bei einer Lackierung, oder als Prozessluft direkt in einem technischen Verfahren wie etwa beim Trocknen, oder als Medium für Prüfprozesse, also als Prüfluft. Das Basiswissen über die Druckluft, ihre Erzeugung, Verteilung und Nutzung gehört zu den wichtigsten Grundlagen der Pneumatik.
Der Aufbau einer Druckluftanlage
4 Teilsysteme gehören zu einer Druckluftanlage.
Die Erzeugung der Druckluft:
Nach dem Ansaugen wird die Umgebungsluft in einem Kompressor zusammengepresst.
Aufbereitung:
Wegen der Schmutz- und Staubpartikel und der Feuchtigkeit der Luft wird die Druckluft gefiltert und getrocknet.
Verteilung:
Spezielle Rohre und Schlauchleitungen führen die komprimierte Luft ihrem Bestimmungsort zu.
Nutzung:
Technisch genutzt wird Druckluft in unterschiedlicher Weise, so z. B. als Linearantrieb, für Motoren oder als Aktivluft bei Lackierarbeiten.
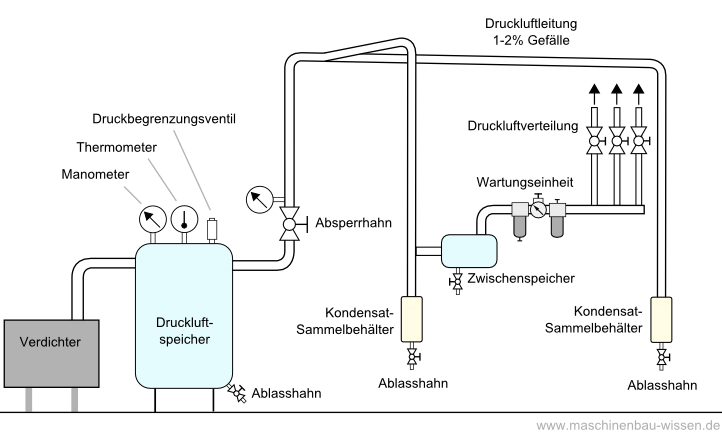
Schematische Darstellung einer gesamten Druckluftanlage mit den wichtigsten Elementen
Anwendungsgebiete der Pneumatik
Pneumatische Anlagen dienen
1. als Linearantriebe (Zylinder). Hier werden Teile gespannt, ausgeworfen und verschoben 2. zum Schalten von Ventilen, beispielsweise von Hydraulikventilen, mithilfe eines pneumatisch funktionierenden Pilotventils 3. als Druckluftmotoren für Schleif-, Bohr- und Schraubmaschinen 4. für Düsen, die Trocknungs- oder Ausblasarbeiten ausführen 5. zur Oberflächenbeschichtung, z. B. zum Lackieren durch Spritzen.
Höhe des Drucks in pneumatischen Systemen
Die Höhe des Luftdrucks, mit der herkömmliche Druckluftanlagen arbeiten, liegt etwa beim Siebenfachen des normalen Atmosphärendrucks. Das sind 6 bar Überdruck (Relativdruck). Hochdrucknetze, die für pneumatische Anwendungen mit hohem Kraftbedarf ausgelegt sind, haben ein deutlich höheres Druckniveau, und zwar bis zu 18 bar. Dafür müssen jedoch spezielle Bauteile wie Schläuche und Verbindungsstück verwendet werden, die diesen hohen Druck aushalten. In besonderen Anlagen, wie z. B. bei Anlagen zur Herstellung von PET-Flaschen, kann die Höhe des Drucks im Druckluftnetz weitaus höher liegen, bis zu einem Niveau von 40 bar.
Weitere Infos zu den Grundlagen der Pneumatik finden Sie in den einzelnen Artikeln des Online-Skript.
Pneumatik-Systeme werden in Anlagen und Maschinen wegen ihrer Vorteile, die sie bieten, eingesetzt. Dabei steht die Pneumatik häufig in Konkurrenz zur Hydraulik oder auch einer rein elektrischen Lösung. Die Kenntnis über die Vorteile der Pneumatik gegenüber der Hydraulik oder Elektrik sind wichtig, wenn es um die Entscheidung für eines der Systeme geht.
Letztendlich hat jede Technologie ihre eigenen Vorteile und Nachteile, daher muss man von Fall zu Fall abwägen, welche Lösung die beste ist. Häufig wird auch eine Mischlösung verwendet, bei der Elektrik, Pneumatik und Hydraulik zusammenspielen.
Vorteile der Pneumatik
- stufenlose Schaltung beziehungsweise Regelung der Geschwindigkeiten und der Kräfte der Zylinder
- Erreichung enorm hoher Arbeitsgeschwindigkeiten (bei einem Standardzylinder bis zu 1500 mm/s, bei einem Hochleistungszylinder bis zu 3000 mm/s und bei Motoren bis zu 100.000 min-1)
- bei einer Überlastung bis hin zum Stillstand haben Druckluftgeräte den Vorteil in der Regel schadlos zu bleiben
- im Vergleich zu Elektrogeräten sind Druckluftgeräte einfach konstruiert; aus diesem Grund im Allgemeinen leichter, wodurch sich die körperliche Belastung der in der Herstellung tätigen Mitarbeiter mindert
- anders als bei elektrischen Systemen, fällt bei pneumatischen Systemen die Abwärme nicht an den dezentralen elektrischen Antriebseinheiten, sondern ausnahmslos zentral am Kompressor selbst
- während Arbeitsmedien von elektrischen Systemen (wie beispielsweise Hydrauliköl) Kosten verursachen, ist Luft als Arbeitsmedium pneumatischer Systeme - zumindest in einem nicht aufbereiteten Zustand - stets und kostenlos vorhanden
- pneumatische Systeme benötigen keine Rückleitungen, da die entstehende Abluft direkt in die Umgebung entweichen kann; die Folge sind einfache Topologien von Druckluftleitungssystemen
- durch eine periodische Kontrolle der Druckluftbehälter des pneumatischen Systems wird Explosionssicherheit gewährleistet
- Unempfindlichkeit der Druckluft gegenüber atomarer Strahlung und magnetischen Impulsen
- Speicherung von Energie in Form von Druckluft möglich
Der Einsatz von Druckluft bietet zahlreiche Vorteile im Vergleich zu anderen Antriebstechnologien. Doch es sind auch Nachteile mit der Anwendung von Pneumatik verbunden. Ein Bewusstsein für die Nachteile der Pneumatik gegenüber der Hydraulik oder Elektrik sind wichtig, wenn man sich für eines der Systeme entscheiden muss.
- Energieverlust
Der Wirkungsgrad der eingesetzten Energie ist bei Druckluftanlangen weitaus niedriger, als wenn elektrischer Strom direkt für Antriebe eingesetzt wird. Der Grund dafür liegt darin, dass für die Verdichtung der Luft am Kompressor ein bestimmter Energieaufwand nötig ist. Ein erheblicher Teil der Energie wird dabei in Wärme umgesetzt. Trotz der anschließenden Wärmerückgewinnung geht beim Prozess der Luftverdichtung insgesamt Exergie verloren.
- Kälte
Druckluftmotoren und andere pneumatische Komponenten, die schnell mit Luft durchströmt werden, kühlen beim Betrieb ab. Sie können sogar vereisen.
- Begrenztheit der Kräfte im Vergleich zu hydraulischen Antrieben
Die Kolbenkräfte sind begrenzt. Die Ursache liegt darin, dass der Betriebsdruck sich meist unter 12 bar bewegt. So entwickelt beispielsweise ein Kolben mit dem Durchmesser von 200 mm bei 7 bar eine theoretische Kraft von 21000 N (ca. 2100 kg).
- Gleichförmigkeit der Kolbengeschwindigkeit erfordert besondere Technik
Ein weiterer Nachteil der Pneumatik ist, dass besondere Dichtungs- und Drosselungstechnik erforderlich ist, um gleichförmige Kolbengeschwindigkeiten zu erreichen (Sinus-Zylinder).
- Herstellung von Festanschlägen erforderlich
Wegen der Kompressibilität der Luft ist das genaue Anfahren einer bestimmten Position bzw. sind genaue Stellungen nur durch Festanschläge möglich.
- Lärm
Pneumatische Anlagen verursachen Lärm durch die ausströmende Druckluft. Als Gegenmaßnahmen müssen Schalldämpfer eingeplant werden.
- Kosten
Nachteile der Pneumatik sind auch, dass die Aufbereitungsprozesse der Druckluft aufwendig sind und erhebliche Kosten verursachen. Beim Aufwand an eingesetzter Energie liegt noch ein Sparpotential.
- Die Druckluft muss aufbereitet werden
Druckluft enthält zunächst Schmutz und Feuchtigkeit. Sie muss in vielen Fällen aufwendig aufbereitet werden.
- Ölgehalt der Atemluft
Es können Aerosole in die Atemluft gelangen, das bedeutet eine erhöhte Ölkonzentration am Arbeitsplatz. Dieser Nachteil wird vermieden, wenn bei neueren Pneumatikelementen auf Druckluft mit Ölgehalt verzichtet wird. Sie werden mit einer Dauerschmierung ausgestattet und kommen ganz ohne Öl aus. Dadurch wird eine hohe Lebensdauer der Bauteile gewährleistet. Wenn aufgrund bestehender Pneumatiknetze ölhaltige Luft nicht zu vermeiden ist, können in die Abluftelemente Ölabscheider installiert werden.
- Wartung und Kosten
Die Wartungskosten einer pneumatischen Anlage sind ein großer Nachteil dieser Technologie. Regelmäßige gründliche Wartung ab einer bestimmten Baugröße ist deshalb sehr wichtig, weil platzende Pneumatikspeicher riesige Gasvolumina freisetzen und dies katastrophale Auswirkungen haben kann, vor allem innerhalb geschlossener Räume. Es besteht eine Prüfungspflicht, die mit regelmäßigen Zusatzkosten verbunden ist.
- Lecks sind schwierig zu lokalisieren
Im Vergleich zu Starkstromleitungen sind bei Druckluftnetzen Lecks sehr schwierig oder gar nicht zu lokalisieren. Ein Leck kann über lange Zeiträume unentdeckt bleiben und die Energiekosten deutlich erhöhen.
Komprimierte Luft, im Alltag auch Pressluft genannt, ist sogenannte Druckluft. Sie wird in der Pneumatik folgendermaßen eingesetzt:
- als Träger für Energie, etwa für Antrieb im Untertage-Bergbau
- in der Signalübertragung analog zum elektrischen Strom
- für Reinigungszwecke
- als Gas zum Atmen
- als Kühlmittel
- zur Stickstoffproduktion
Wenn man nicht Luft, sondern besondere Gase oder auch Gemische benutzt, nennt man diese Druckgase.
Luft – Definition & Zusammensetzung
Das Gasgemisch unserer Erdatmosphäre bezeichnet man als Luft. Luft in trockenem Zustand enthält überwiegend die Gase Stickstoff mit ca. 78,08 Volumen-% und Sauerstoff mit ca. 20,95 Volumen-%. Der Rest sind Argon mit 0,93 Volumen-%, Kohlenstoffdioxid mit 0,04 Volumen-% und Spuren anderer Gase. Wasser in Gasform, also Wasserdampf, liegt durchschnittlich mit 1,3 Volumen-% nahe dem Erdboden und zu 0,4 Volumen-% in der sonstigen Erdatmosphäre vor, wurde bei den oben genannten Werten aber nicht berücksichtigt. Luft ist normalerweise ohne Geruch, Farbe und Geschmack.
Herstellung von Druckluft
Je nach geplanter Verwendung kann Luft in der Pneumatik durch Verdichter, sogenannte Kompressoren, unter erhöhten Druck gesetzt und anderweitig behandelt werden. Komprimieren erfordert hohen Energieaufwand, da Wärmeenergie dabei ungenutzt entweicht. Bisher war Druckluft deshalb ein teurer Träger von Energie. Durch neue energiesparende Verfahrenstechniken fällt die Kostenbilanz für Druckluft heute besser aus: Mittels Wärmerückgewinnung und Leckvermeidung können auch viel CO2 eingespart und die Herstellungskosten gesenkt werden.
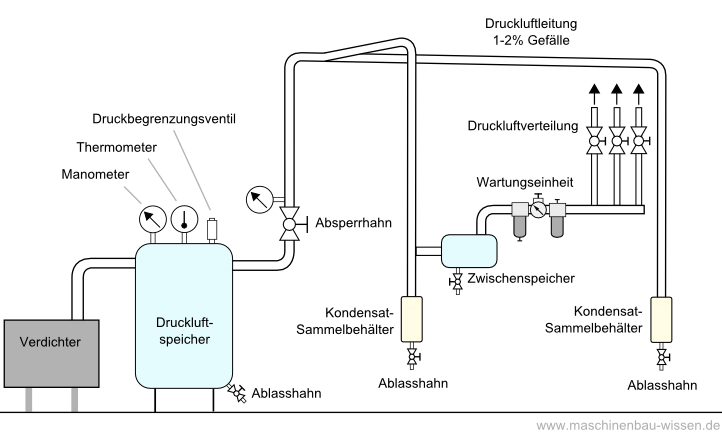
Schematische Darstellung einer gesamten Druckluftanlage mit den wichtigsten Elementen
Die Herstellung von Druckluft basiert meist auf zwei unterschiedlichen Verfahren: Ein meist zweistufiger Kolbenkompressor oder Schraubenverdichter bzw. dreistufige Kolbenkompressoren können einen Verdichtungsdruck von 3000 bar erzeugen. Ebenso kommen Rotationskompressoren und zum Teil auch Membrankompressoren zum Zuge. Die Kompressorleistung wird angegeben mit l/min bzw. m³//h und stellt die sogenannte Lieferleistung des Kompressors dar.
Druckluftverteilung
Druckluft wird also erzeugt, gespeichert, aufbereitet und genutzt. Die wichtigste Komponente in der Pneumatik aber ist die Verteilung in der Druckluftanlage. In vielen Installationen wird dies, da technisch vermeintlich nicht anspruchsvoll, häufig vernachlässigt. Hohe Betriebskosten entstehen jedoch gerade bei der unsachgemäßen Druckluftverteilung in Systemen in Planung als auch Ausführung.
Verwendungsdruck
Wenn Druckluft zur Reinigung oder als Energieträger verwendet wird, braucht man einen Druck von 6 bis 8 bar, manchmal sogar bis 16 bar. Beim Tauchen oder in Atemschutzgeräten wird die Atemluft in Flaschen oder Kartuschen bei 200 bis 300 bar verwendet. Spezielle aus Carbon gefertigte Behälter halten Drücken von 300 bar stand und sind Herzstück etwa von transportierbaren Druckluftwerkzeugen, beispielsweise zum Nageln, oder auch in sogenannten Luftgewehren. Werden Schüttgüter gefördert mit Hilfe der Pneumatik, braucht man Drücke von bis zu 4,5 bar.
Als Luftdruck bezeichnet die Wissenschaft den Druck, welcher von einer Luftmasse unter Einwirkung der Erdanziehungskraft auf die Erdoberfläche ausgeübt wird. Laut Definition ist der Luftdruck das Luftsäulengewicht pro Flächeneinheit, gemessen vom Erdboden bis zum äußeren Rand der Atmosphäre. Die Messung des Luftdrucks erfolgt mittels Barometer.
Physikalische Einheit
Die standardisierte Maßeinheit für den Luftdruck lautet hPa (Hektopascal). Früher wurde der Luftdruck in Bar angegeben, wobei ein hPa 1 mbar entspricht.
Es gilt: 1 hPa = 100 Pa = 1 mbar = 100 N / qm = 100 kg / (m qs)
(mit: qm= Meter zum Quadrat und qs= Sekunde zum Quadrat)
Druck Umrechnungs-Tabelle
Mit Hilfe der folgenden Druck-Umrechnungs-Tabelle kann man verschiedene Einheiten für Druck in eine beliebige andere Einheit einfach umrechnen.
Der atmosphärische Druck
Die Masse der Erdatmosphäre beträgt circa 5,15*1018 kg. Das bedeutet: Auf jedem Quadratmeter Erdoberfläche lasten etwa 10 Tonnen. Auf Höhe des Meeresspiegels beträgt der Druck (Angabe in Kraft pro Fläche) 105 N/m². In höheren Lagen bleibt ein Teil der Luftsäule unterhalb des jeweils betrachteten Niveaus, weshalb der gemessene Luftdruck mit zunehmender Höhe sinkt. So erreicht er beispielsweise über Mitteleuropa in 5500 Metern Höhe über NN circa 500 hPa.
Nimmt die Höhe weiter zu, wird die Druckabnahme immer weniger deutlich. Das erklärt sich vor allem dadurch, dass die unteren atmosphärischen Luftschichten dichter und damit schwerer sind als die oberen.
Um Luftdruckverhältnisse in bestimmten Höhen kartografisch annähernd genau erfassen zu können, verwenden Wissenschaftler das sogenannte Geopotential. Dabei handelt es sich um eine Methode, mit deren Hilfe sich Höhenluftdrücke auf Basis der Boden-Luftdruck-Karten recht genau ableiten lassen.
In Meereshöhe beträgt der mittlere Luftdruck genau 1013,25 hPa, was etwa 1 bar entspricht. Laut standardisierter Werte verringert sich der Druck bis in 5,5 km Höhe auf 500 hPa, während er in rund 30 km Höhe auf 10 hPa abfällt.
Hochdruck und Tiefdruck
Sofern der aktuelle Luftdruck unter oder über dem ortsüblichen Luftdruck liegt, spricht man von Tief- bzw. von Hochdruck. Die Schwankungsbreite der Luftdruckverhältnisse auf der Erde ist recht gering. Der höchste Luftdruck wurde 1968 in Sibirien gemessen (1080 hPa). Der jemals beobachtete niedrigste Luftdruckwert stammt aus dem Jahr 1927. Er wurde auf den Philippinen, unmittelbar während eines Taifuns gemessen. Der Grund für diese relativ kleinen Schwankungen besteht darin, dass Luftdruckunterschiede keine stabilen Systeme darstellen. Sie tendieren immer dazu, sich schnellstmöglich wieder auszugleichen.