Der Ausdruck Kalander stammt vom französischen Begriff "calandre" für Rolle. Es handelt sich bei einem Kalander um ein System aus mehreren aufeinander angeordneten Rollen. Sie sind beheizt und poliert und werden in der Regel aus Stahl oder Schalenhartguss gefertigt.
Funktionsweise Kalandrieren
Durch die Spalten der Walzen werden die Kunststoff-Schmelze oder auch andere Materialien hindurchgeführt. Das Kalandrieren dient der Herstellung von verschiedensten Folien aus Kunststoff sowie aus Metallen, Gummi und Papier. Als Kunststoffe werden für das Verfahren Kalandrieren unter anderem PVC, PE und PS eingesetzt. Typische Metallfolien bestehen etwa aus Zinn oder Aluminium.
Unterscheidungsmerkmale verschiedener Kalanderarten
Generell kann zwischen Schmelzkalandern und Beschichtungskalandern unterschieden werden. Die Ersteren dienen der Herstellung von Folien, während Letztere zur Beschichtung verschiedener Gewebe-Produkte, wie etwa Transportbändern, verwendet werden. Auch unterscheidet man hinsichtlich der Bauform des jeweiligen Kalanders. Diese Unterscheidung wird anhand der Positionierung der Walzen in der Seitenansicht der Maschine vorgenommen. Übliche Bauformen sind zum Beispiel I-, F-, L- und Z-Kalander.
Die verschiedenen Kalanderarten
Wie bereits beschrieben wird anhand der Walzenanordnung und der Art der Materialzuführung zwischen verschiedenen Kalander-Arten unterschieden. In der PVC-Hartverarbeitung kommt hauptsächlich der L-Kalander zum Einsatz. Für die PVC-Weich-Verarbeitung ist die F-Form üblich, während Gewebebahnen meist auf der Z-Form kalandriert werden.
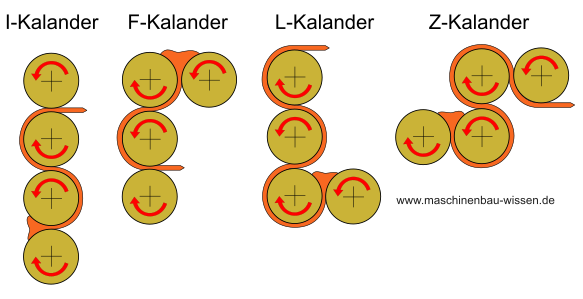
Darstellung der vier wichtigsten Arten von Kalandern
Welche Vor- und Nachteile hat das Kalandrieren auf den verschiedenen Bauarten?
Vierwalzen-I-Kalander
Da diese Art von Kalander mit erheblichen Nachteilen bei der Beschickung behaftet ist, kommt sie heute kaum noch zum Einsatz.
Vierwalzen-F-Kalander
Eignet sich sehr gut für PVC-Weich-Bearbeitung. Denn Weichmacher-Dämpfe steigen nach oben ohne die Walzen und somit die Folien zu berühren. Denn bei dieser Bauart wird die Formmasse von oben zugeführt.
Vierwalzen-L-Kalander
Hier befindet sich der Spalt für den Massedurchlauf unten. Er lässt sich daher problemlos auf dem kürzesten und einfachsten Weg beschicken. Daher wird er vorzugsweise für die Hart-PVC-Bearbeitung genutzt. Dem entgegen steht die Problematik, dass bei der PVC-Weich-Bearbeitung Dämpfe von Weichmachern zur Folie hinter den obersten Walzen aufsteigen. Diese beeinflussen die Qualität der Folie negativ.
Vierwalzen-Z-Kalander
Diese Bauform ist die zweckmäßigste zum Einarbeitung von Beschichtungen in Gewebebahnen
Der übliche Bereich für Dicken bei kalandrierten Folien liegt zwischen 30 und 800 Mikrometern. Bodenbeläge (PVC, CV) können von speziellen Kalandern jedoch auch in größeren Stärken hergestellt werden. Für die Herstellung von Folien aus u-PVC setzt man üblicherweise die L-Bauform ein, während für Folien aus p-PVC normalerweise die F-Form genutzt wird.
Für das Kalandrieren geeignete Formmassen
Nahezu alle Thermoplaste können kalandriert werden. Voraussetzung ist, dass sich der verwendete Kunststoff durch eine hohe Viskosität auszeichnet, da es sonst zu Problemen im Fertigungsprozess kommen kann. Am häufigsten werden PVC mit und ohne Weichmacher sowie Copolymere von PVC zum Kalandrieren verwendet. Weiterhin werden aus schlagzähem PS und ABS kalandrierte Produkte hergestellt. Darüber hinaus eignen sich viele Polyoefine sowie Zelluloseester.
Der Maschinenaufbau des Kalanders
Maschinentechnische Begriffsdefinition
Unter dem Begriff Kalander versteht man ausschließlich das Maschinengehäuse mit den Walzen, die Antriebsmotoren sowie deren Steuerung bzw. die elektronischen Komponenten zur Regulierung und Einstellung der Anlage. Die Kalanderstraße hingegen bezeichnet die komplette Anlage zur Fertigung von Folien.
Besonderheiten bei der Konstruktion eines Kalanders
Bei der Konstruktion und Auslegung eines Kalanders ist auf einiges zu achten. Die Kalanderwalzen sind achsenparallel angeordnet und befinden sich in einem robusten Rollenlager. Dadurch ist eine sehr hohe Rundlaufgenauigkeit gewährleistet. Für die Fertigung unterschiedlicher Produkte sind die Abstände der einzelnen Walzen zueinander exakt einstellbar.
Die Enden der Kalanderwalzen sind unterschiedlich ausgeprägt. An einem Ende befindet sich ein sogenannter Rotary-Anschluss. Dieser ermöglicht das Heizen bzw. Kühlen der Walze. Am anderen Ende befindet sich eine Kupplung zur Antriebsachse. Der Antrieb erfolgt einzeln pro Walze. Hierfür wird jeweils ein Motor verwendet, der direkt mit dem Getriebeblock der Maschine verbunden ist.
Kalanderwalzen bestehen aus Stahl oder Verbundguss. Sie erreichen eine Oberflächenhärte von etwa 500 bis 580 HB. Dies ist notwendig, denn zum einen wird eine extrem verschleißfeste Oberfläche benötigt, zum anderen müssen die Walzen bei der Kunststoff- und Metall-Verarbeitung hohe Zähigkeit und Festigkeit aufweisen sowie hohe Spaltkräfte aufnehmen.
Maßnahmen zur Verhinderung von Maßabweichungen beim Kalander
Zwischen den Walzenspalten treten während des Produktionsprozesses große Kräfte auf. Dadurch werden die Kalanderwalzen leicht durchgebogen. Dies kann zu Maßabweichungen bei den hergestellten Folien führen. Diese Maßabweichungen lassen sich zumindest teilweise kompensieren. Hierfür kann eine Schrägstellung der Walzen oder eine Gegenbiegung erfolgen. Durch die Schrägverstellung versetzt man die Achse der vorletzten Walze im Kalander. Dadurch erreicht man, dass der entstehende Spalt an den Walzenenden breiter ist als in der Mitte der Walzen.
Das sogenannte Roll Bending (also die Gegenbiegung) nimmt man an der letzten Walze vor. Sie geschieht durch hydraulische Kräfte, welche auf Hilfslager einwirken, die sich an den Zapfen der Walzen befinden.
Nicht immer reichen diese beiden Maßnahmen aus, um die entstandenen Maßabweichungen zu korrigieren. Daher erfolgt in diesen Fällen zusätzlich ein Profilschleifen der letzten beiden Walzen im aufgeheizten Zustand.
Konstruktion und Herstellung von Kalandern
Ingenieure sehen sich bei der Konstruktion von Kalandern regelmäßig verschiedenen Problemstellungen ausgesetzt. Zunächst muss sich der Abstand zwischen den einzelnen Kalanderwalzen extrem präzise regeln lassen. Außerdem sollen die Walzen so wenig Masse wie möglich besitzen und dabei eine möglichst große Breite aufweisen. Zugleich sollen sie jedoch hohem Druck Stand halten.
Aufgrund dieser Anforderungen lässt es sich meist nicht vermeiden, dass im Produktionsprozess die genannten Biegeeffekte auftreten, die zu Maßungenauigkeiten bei der Kunststoff- und Metall-Folienherstellung führen können. Weiterhin kann es zu thermischen Verformungen der Walzen kommen. Dies versuchen die Konstrukteure durch eine kalkulierte Abweichung vom zylindrischen Walzenprofil auszugleichen. Es werden Tonnenprofile eingesetzt, die ballig geschliffen sind. Sie sind daher in der Mitte leicht verdickt. Auch möglich ist der Einsatz zweier gegenläufiger Trapez-Profile oder von S-Profilen. Die Verdickung wird alternativ als Bombage bezeichnet. Mit den beiden letztgenannten Profilen geht der Vorteil einher, dass sich durch Veränderung der Walzenlage Abstandsfeinregulierungen vorgenommen werden können. Hierfür können die Walzenabstände parallel oder geschränkt verändert werden.