Fluidtechnik - Skript
In diesem Fluidtechnik-Skript lernt man mehr über die verschiedenen Maschinen-Elemente, die zum Betrieb von hydraulischen und pneumatischen System notwendig sind – wie zum Beispiel Pumpen, Filter, Ventile, Zylinder und mehr.
Häufig verwendete Komponenten in der Fluidtechnik sind:
- Speicher (Druckbehälter, Gasflasche, Druckluftbehälter, Tank etc.)
- Pumpe
- Zylinder
- Motor
- Mess- und Anzeigegeräte (Manometer, Termperaturmesser, Volumenstrommessgerät etc.)
- Rohre
- Schläuche
- Kugelhähne
- Wegeventile
- Sperrventile
- Druckventile
- Filter
- Wärmetauscher
- Heizung
- Kühler
- Wartungseinheit
- Lufttrockner
- Öler
- Schalldämpfer
Eine Hydraulikpumpe hat als Bauelement in einer hydraulischen Anlage die Aufgabe, die Druckflüssigkeit zu fördern. Dabei soll die Hydraulikpumpe einen bestimmten kontinuierlichen Volumenstrom erzeugen und gegebenenfalls Druck erzeugen.
Die Wichtigsten Parameter einer Hydraulikpumpe sind daher der Druckbereich (zumeist in bar) und die Förderleistung (zumeist in L/min oder m3/h).
Bei den Hydraulikpumpen existieren folgende Bauformen:
a) Umlaufverdränger
- Verdrängelement = Zahn:
- Zahnradpumpe – Link Wikipedia
- Außenzahnradpumpe
- Innenzahnradpumpe
- Zahnringpumpe
- Zahnradpumpe – Link Wikipedia
- Verdrängelement = Schraube:
- Schraubenspindelpumpe – Link Wikipedia
- Verdrängelement = Flügel:
- Flügelzellenpumpe bzw. Drehschieberpumpe – Link Wikipedia
- Sperrschieberpumpe
b) Hubverdränger
- Verdrängelement =Kolben:
- Reihenkolbenpumpe
- Radialkolbenpumpe – Link Wikipedia
- mit innerer Kolbenabstützung
- mit äußerer Kolbenabstützung
- Axialkolbenpumpe – Link Wikipedia
- Taumelscheibenpumpe
- Schrägscheibenpumpe – Link Wikipedia
- Schrägachsenpumpe – Link Wikipedia
- Verdrängelement = Membran:
- Membranpumpe – Link Wikipedia
Ein Verdichter, oder auch Kompressor, wird zur Komprimierung von Gasen verwendet und gehört zu den Fluidenergiemaschinen.
Grundlagen rund um den Druckluft-Verdichter
Wird das Volumen eines Gases verringert, so bezeichnet man diesen Vorgang als Verdichtung oder auch Komprimierung. Die hierzu benötigten Maschinen werden Verdichter oder Kompressoren* genannt. Während des Vorgangs der Verdichtung wird das vorhandene Ansaugvolumen (V1) mit einem Betriebsdruck (p1) zusammengepresst und somit im Umfang verringert zu einem kleineren Volumen (V2). Innerhalb des nun kleineren Volumens besteht ein höherer Druck (p2). Das Gas wird während des Prozesses der Verdichtung zudem erwärmt.
Aufgrund der Komprimierung des Volumens während des Vorgangs der Verdichtung, ist es wichtig, den Druckzustand des Volumenstroms zu nennen. Üblicherweise werden hier der Saugvolumenstrom, der Austrittsvolumenstrom in Bezug auf den Enddruck p2, oder auch der Normvolumenstrom als Angabe herangezogen.
Aufbau & Funktion eines Kolbenverdichters
Bei konstanter Temperatur gilt bei Verdichtungsvorgängen im Kompressor das Boyle-Mariottesche Gesetz.
Findet dieses Gesetz Anwendung, muss beachtet werden, dass es sich bei p1 und p2 um absolute Drücke handelt. Die Druckangaben pneumatischer Anlagen und pneumatischer Druckmessgeräte sind jedoch auf das Verhältnis von Überdruck Pe zu atmosphärischem Druck bezogen. In anderen Fällen findet eine gesonderte Kennzeichnung der Druckangaben statt.
Betriebsdruck und Liefermenge vom Kompressor
Erreichbarer Druck und Liefermenge vom Kompressor dienen seiner Kennzeichnung. Die Liefermenge ist hierbei definiert als das abgegebene Luftvolumen je Zeiteinheit und wird zumeist in m3/min angegeben. Lediglich bei kleineren Anlagen werden die Angaben in Liter/min gemacht.
Häufig wird auch die Angabe einer theoretischen Ansaugleistung gebraucht, welche jedoch irreführend sein kann. Hierbei wird die Ansaugleistung als Produkt aus Hubvolumen und Drehzahl angegeben, ohne dass eine Aussage über die tatsächliche Fördermenge getroffen wird, da der volumetrische Füllungsgrad nicht weiter betrachtet wird.
Unterscheidung von Verdichtern
Es wird in Turboverdichter und Verdrängerverdichter unterschieden. Während Turboverdichter große Volumenströme an Druckluft liefern, bei nur kleinen Verdichtungsenddrücken, zeichnen sich Verdrängerverdichter aus durch einen kleinen Durchsatz und große Verdichtungsenddrücke.
Auch lassen sich Kompressoren in ölgeschmierte und ölfreie Verdichter unterteilen.
Im Bereich der Kältetechnik findet zudem eine Unterscheidung in vollhermetische, halbhermetische und offene Verdichter statt. Befinden sich beim vollhermetischen Kompressor Motor und Verdichter in einem speziell abgeschlossenen Gehäuse in direktem Kontakt mit dem jeweiligen Kältemittel, zeichnen sich halbhermetische Kompressoren dadurch aus, dass der Motor an das Gehäuse des Kompressors angesetzt ist. Bei offenen Verdichtern findet der Antrieb durch Riemen, Zahnräder oder ein Getriebe statt.
Bauformen von Kompressoren
Verdichter sind in unterschiedlichen Bauformen zu finden und eingesetzt.
Es wird unterschieden in Schraubenverdichter, Hubkolbenverdichter, Labyrinth-Kolben-Verdichter, Turboverdichter, ionische- und Lamellenverdichter, wie auch Rotations- und Schraubenverdichter. Weiterhin finden sich im Gebiet der Kompressoren die Flüssigkeitsringpumpe, der Taumelscheibenverdichter, im Englischen auch Wobble-Plate genannt, das Roots-Gebläse, Swash-Plates (Schiefscheibenverdichter), Scrollverdichter, Seitenkanalverdichter, Membranverdichter und auch Junkers-Freikolbenverdichter.
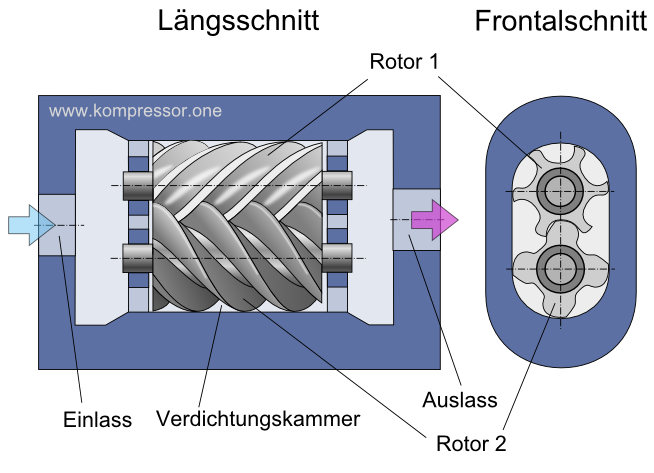
Aufbau von einem Schraubenverdichter
Relevante Kenngrößen
Wichtige Kenngrößen vom Kompressor sind die Liefermenge als Volumen des ausgestoßenen Fluids pro Zeiteinheit, wie auch der Betriebsdruck, der durch den erreichbaren Überdruck der Druckluft beschrieben wird. Ebenfalls eine relevante Kenngröße ist das Druckverhältnis, das sich aus der Beziehung von Enddruck zu Saugdruck ergibt. Der Liefergrad gibt das Verhältnis zwischen gefördertem und in der Theorie möglichem Volumenstrom der Druckluft an.
Der Vergleich verschiedener Kompressoren wird unter Betrachtung des Normvolumenstroms vollzogen. Hierbei handelt es sich um den Volumenstrom, der auf Normbedingungen in Temperatur, Druck und Luftfeuchtigkeit umgerechnet wird.
Auf dieser Seite wird beschrieben, wie man die Größe von einem Kompressor* bestimmen kann. Die Kompressor-Größe ist dabei von unterschiedlichen Faktoren abhängig und es sind somit mehrere Schritte erforderlich, bis man die ideale Dimensionierung des Drucklufterzeugers ermittelt hat.
1. Kompressor-Bauart bestimmen
Bei der Anschaffung eines Kompressors muss zunächst die Entscheidung für die entsprechende Bauart fallen. Die Optionen sind hierbei zumeist auf die Frage beschränkt, ob es ein Kolbenkompressor oder ein Schraubenkompressor werden soll. Beide Bauarten weisen bestimmte Vorteile auf, auf Basis derer die Entscheidung fällt.
Schraubenkompressoren haben vor allem den Vorteil einer großen Liefermenge und eines pulsationsfreien Volumenstrom. Kolbenkompressoren eigenen sich hingegen besser bei intermittierendem Bedarf und zur Kompensation von Lastspitzen. Zudem ist es mit einem Kolbenkompressor auch möglich Höchstdrücke von bis zu 35 bar zu erreichen.
Wenn die Entscheidung nach der Bauart des Verdichters gefallen ist, startet man mit der Ermittlung des Kompressor-Höchstdrucks.
2. Maximalen Kompressor-Druck berechnen
Der maximale Kompressor-Druck – auch Höchstdrück – ergibt sich aus mehreren Einflussgrößen. Hierzu zählen der höchste Arbeitsdruck der Druckluftverbraucher und die Summe der Druckverluste, die im Druckluftnetz auftreten. Auch zu berücksichtigen ist die Schaltdifferenz, also die beiden Drücke zwischen denen der Kesseldruck im maximalen und minimalen Bereich pendelt.
Schaltdifferenz eines Kompressors (pmax – pmin)
3. Größe des Druckluftbehälters bestimmen
Zur Bestimmung der optimalen Kompressor-Größe gehört auch die Ermittlung des optimalen Druckluft-Behälter-Volumens. Hierfür existieren unterschiedliche Berechnungsformeln, die auch auf Erfahrungswerten beruhen. Bei der folgenden Berechnung kann außerdem auch das Druckluftnetz selbst als Teil des Druckluft-Behälters (auch Kessel) betrachtet werden:
VB - Volumen des Druckluftbehälters [ m³ ]
Q - Liefermenge des Kompressors [ m³/min ]
LB - Benötigte Liefermenge [ m³/min ]
z - Zulässige Motorschaltspiele/h [ 1/h ]
pmax - Ausschaltdruck des Kompressors [ barü]
pmin - Einschaltdruck des Kompressors [ barü]
Bei anderen Methoden zur Berechnung des Druckluftbehälter-Volumens wird zwischen Kolbenkompressor und Schraubenkompressor differenziert:
VB - Volumen des Druckluftbehälters [ m³ ]
Q - Liefermenge des Kompressors [ m³/min ]
15 bzw. 5 - Konstanter Faktor
z - Zulässige Motorschaltspiele/h [ 1/h ]
Δp - Druckdifferenz EIN/AUS
Ein wichtiger Grund für die passende Dimensionierung eines Druckluftbehälters, ist die Schonung des Kompressors. Denn je bei einem zu kleinen Volumen, muss der Drucklufterzeuger immer wieder anlaufen. Dies führt zur stärkeren Abnutzung des Motors. Ein zu großer Kessel kostet mehr und nimmt mehr Raum ein.
Ferner sollte bei der Wahl des Behälters stets ein Behälter aus der Normreihe verwendet werden – also ein Standard-Behälter. Auch auf den maximal zulässigen Druck muss man aus Gründen der Sicherheit achten. Der maximal zulässige Druck des Kessels sollte mindestens 1 bar über dem maximalen Kompressor-Druck liegen.
4. Schaltintervall des Kompressors
Das Schaltintervall wird zur Überprüfung der korrekten Größe des Druckluftbehälters ermittelt. Im Hinblick auf das Schaltintervall stellen die Liefermenge des Kompressors und der Druckluftverbrauch im Druckluftsystem die wichtigsten Einflussfaktoren bei der Größenbestimmung des Kessels dar. Die Berechnung des Schaltintervalls erfolgt dann durch Addition der Kompressorlaufzeit tL und der Kompressorstillstandszeit tS.
Formel zur Berechnung der Kompressorstillstandszeit:
tS - Stillstandszeit des Kompressors [ min ]
VB - Volumen des Druckluftbehälters [ l ]
LB - Benötigte Liefermenge [ l/min ]
pmax - Ausschaltdruck des Kompressors [ barü ]
pmin - Einschaltdruck des Kompressors [ barü ]
Formel zur Berechnung der Kompressorlaufzeit:
tL - Laufzeit des Kompressors [ min ]
VB - Volumen des Druckluftbehälters [ l ]
LB - Benötigte Liefermenge [ l/min ]
Q - Liefermenge des Kompressors [ m³/min ]
pmax - Ausschaltdruck des Kompressors [ barü ]
pmin - Einschaltdruck des Kompressors [ barü ]
Die Berechnung des Schaltintervalls des Kompressor-Antriebs erfolgt dann durch Addition von Kompressorlaufzeit und Kompressorstillstandszeit:
tI - Schaltintervall des Kompressors [ min ]
tL - Laufzeit des Kompressors [ min ]
tS - Stillstandszeit des Kompressors [ min ]
5. Motorschaltspiele berechnen
Der letzte Schritt bei der Auslegung und Dimensionierung von einem Kompressor für die Erzeugung von Druckluft ist die Berechnung der Motorschaltspiele des elektrischen Antriebs. In diesem Schritt wird die Größe des Kompressor-Motors ermittelt.
Wichtig ist das Berechnen der Motorschaltspiele deshalb, weil die maximal zulässige Anzahl an Motorschalspielen Schäden am Antrieb verursachen kann. Somit wird die Größe von einem Kompressormotor in Abhängigkeit von der erwarteten Lebensdauer und den Einsatzbedingungen (wie Kesselvolumen, Druckluftverluste, Schaltintervall) festgelegt.
Die folgende Tabelle zeigt eine Übersicht über zulässige Motorschaltspiele von Elektromotoren mit unterschiedlicher Leistung:
Tabelle: Motorleistung und zulässige Motorschaltspiele
Motorschalspiele für einen Kompressor berechnen
Die Berechnung der zu erwartenden Motorschalspiele S erfolgt über die Division der Bezugszeit (zumeist 60 min) durch die Summe aus Kompressorlaufzeit tL und Kompressorstillstandszeit tS (= Schaltintervall).
S - Motorschalspiele [ 1/h ]
tL - Laufzeit des Kompressors [ min ]
tS - Stillstandszeit des Kompressors [ min ]
Mit Hilfe von diesem Ergebnis kann man das Druckluftsystem sowie den Kompressor dimensionieren. Wenn die berechnete Zahl der Motorschalspiele über der Zahl der zulässigen Schaltspiele liegt, muss entweder ein größerer Druckluftbehälter eingesetzt werden oder die Schaltdifferenz des Kompressors (pmax – pmin) erhöht werden.